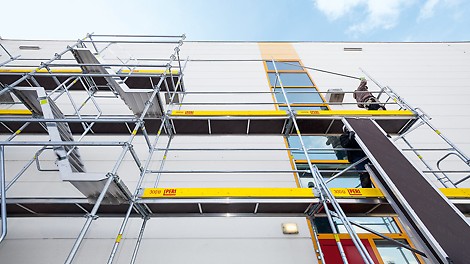
By concentrating on the focal points of efficiency and safety, PERI has aggressively expanded the scaffold technology corporate division in recent years through the addition of new system components and application solutions. Investment in advisory services, engineering and sales are also oriented to conform with the corporate strategy which regards the worldwide prospering growth of the scaffolding sector as a great opportunity for the future. As can be seen by numerous reference projects, the fields of application of PERI UP scaffolding technology are expanding. Except for building and infrastructure construction, PERI scaffold systems in the meantime can now be seen as working platforms and load-bearing constructions in many areas of the manufacturing industry.
With regard to consulting and engineering, an integrated approach is taken in providing support for all scaffolding customers. For this, PERI includes all the experience gained from countless projects around the globe in the design and execution. Scaffolding customer can therefore generally expect not only the best problem-solving expertise but also the optimal solution for each specific challenge. This applies to both the cost-effectiveness as well as safety at all levels because both aspects are basically in the foreground of the entire PERI system technology
PERI holds ready the rentable scaffolding material at over 120 logistics sites worldwide. As a result, the contractor can avoid making any costly investments and instead carry out very transparent calculations for individual, object-related concepts as well as realizing cost-effective implementation. Another advantage is apparent if scaffolding concepts for optimization are supplemented by components taken from the PERI formwork portfolio.
PERI uses the world's leading trade fair, bauma 2016, as the current shop window for showcasing its extensive performance and innovation potential. The company is presenting numerous innovations developed for the PERI UP scaffolding technology – the focus is on the innovative PERI UP Easy* Facade Scaffolding.
* Please note that the German approval by the building authorities for PERI UP Easy has been applied for, but not been granted yet. Until such approval by the building authorities is granted, the application of PERI UP Easy is only allowed with a further individual approval. (Additional note from 29th August 2016)
The new PERI UP Easy* scaffolding system
Next generation facade scaffold
The same question arises ahead of every technical development: is it right to take the next development steps going down the familiar route or use other approaches to achieve new and better solutions? For the new PERI UP Easy* scaffolding system, PERI decided in favour of the latter option. It combines the fast assembly of a frame scaffold with the flexibility of modular scaffolding thereby exploiting the weight advantages of high strength steels. This combination leads to significant safety and erection advantages opening a new dimension for facade scaffolding.
The key to this lies in the constructive centrepiece of the PERI UP Easy* scaffolding system: its open frame with the integrated rosette nodes. Through these nodes, PERI UP Easy* can be combined with the system components of the PERI UP Flex Modular Scaffolding. Apart from possible adaptation to suit complex building geometry, PERI UP Easy* thus offers simple and rapid installation on stair towers, brackets, internal guardrails, roof edge protection scaffold or working platforms.
In addition, a number of new developments determine the efficiency of the scaffolding system; for example, the quick coupling system for connecting to the scaffolding anchors. Without requiring any tools, the coupling is inserted into a longitudinal hole in the frame or on a bracket, and fixed in position by being turned 90°. Also following the principle of the tool-free assembly is the simple corner configuration whereby no couplings are required, likewise the installation of the decking which features the integrated protection against lifting.
Look at the scaffolders
PERI UP Easy* is the result of intensive involvement with the working environment found in scaffolding construction. All conversations and discussions with scaffolders have repeatedly confirmed which working realities scaffold erection teams are confronted with every day. In addition to the generally high risk of accidents and time pressure, it is primarily the lifting and carrying of heavy loads and working in forced postures that are seen as particularly detrimental to a worker´s health. Through the use of high strength steels and the constructive finishing touches, PERI UP Easy* is a "lightweigth" among steel facade scaffolding systems.
Safety and cost-effectiveness should never be a contradiction
On the contrary: working with or on scaffolding always means moving around in a high-risk location. Based on this unalterable fact, PERI has always drawn the only sustainable conclusion in scaffolding construction: not until work safety is improved can the economic efficiency of the entire system be increased.
With the open frame and the resulting guardrail in advance, PERI has succeeded in realizing this quantum leap. As the guardrail for the next scaffolding level is already mounted without any additional components with the Easy* Frame from the level below the scaffolder can move around on all scaffold levels at all times without requiring anti-fall protection.
The frame with the integrated scaffold node merges the boundaries between frame and modular scaffolding. This allows, for example, brackets to be connected directly or scaffold staircases can be installed without any additional frame columns. In all other assembly processes, considerable savings can also be made in each case regarding materials and working time.
Through the use of the proven decking system taken from the PERI UP Flex Modular Scaffolding, the advantages of self-securing decks as well as the very quick Gravity Lock are now also being used with frame scaffolding.
Without limits in new and existing buildings
In addition to the erection speed when working on the facade, the ability to adapt to the contours and geometries of the structure is always a decisive criterion. Projections and recesses in the facade, cantilevered and free-standing structural components: for the scaffolder, all of this can be equally well-managed thanks to the assembly versatility of PERI UP Easy* in combination with PERI UP Flex. In this connection, the metric grid dimensions both in length and width also play an important role. Through the 33 cm decking width, the scaffold decks can be used in both 67 cm as well as metre-wide scaffolding.
* Please note that the German approval by the building authorities for PERI UP Easy has been applied for, but not been granted yet. Until such approval by the building authorities is granted, the application of PERI UP Easy is only allowed with a further individual approval. (Additional note from 29th August 2016)
Safer, faster and now wider
PERI UP Flex Shoring Tower MDS for System Grid 150
The PERI UP Flex Shoring Tower MDS shares its best features with the PERI UP Flex scaffolding system: it can be assembled extremely quickly and offers a high level of constructional safety for users. With a new head frame, it is even more versatile.
Since it was unveiled three years ago, the PERI UP Flex Shoring Tower MDS has proven itself in many applications. During development we paid grat attention to the weight. No component weighs more than 16 kg which saves the energy of site personnel and significantly improves the otherwise very strenuous manual handling.
Safety equipment mounted in advance
In addition, the erection procedure is simplified through the special assembly logic. The decks are transported upwards on the inside, i.e. in the area of the shoring tower already protected, and then mounted on the respective higher-positioned ledgers without tools from a safe working position. Following the same principle, the guardrails are mounted in advance from the lower level in each case. As a result, every new level is already secure before it even being accessed. The reduced weight and assembly without tools accelerate assembly and dismantling significantly.
New grid system, new system accessories
With an extended range of accessories, PERI has opened up new areas of application for the PERI UP Flex Shoring Tower MDS. The most important new component is the new Head Frame MDS 150 which has allowed the MDS standard grid to be extended from 1.25 m to 1.50 m. This means the MDS can be used under formwork systems with larger grid dimensions, e.g. SKYDECK slab panels or slab tables. In addition, a new head spindle is now part of the product portfolio. For ensuring fast horizontal moving, a new connection for the Shoring Tower MDS is available which serves for mounting the proven transportation wheel from the PERI programme.
PERI PEP Alpha
The steel tube slab props for daily use
The new prop family, PEP Alpha, is classified as Class D in accordance with EN 1065 whereby the two prop types, PEP Alpha D-300 and D-350, cover around 80 % of the usual range of applications for steel tube props according to PERI´s own market observations.
The D-300 version reaches extension lengths of 1.80 m to 3.00 m while the larger D-350 model covers the 2.00 m to 3.50 m range. The required load-bearing capacity according to EN 1065 Class D is maintained through to the full extension length and significantly exceeds this with smaller extension lengths. For the PEP Alpha D-300, PERI confirms a load capacity of up to 41.4 kN, with up to 37.5 kN for the D-350. These are exceptional practice-oriented values which show a very positive increase compared with the norm. In comparison with the proven PEP Ergo props, also from PERI, the PEP Alpha props have a more simple design. They do without, among other things, details such as the possibility to repair the prop in favour of a more favourable price.
Upgrade for the PERI UP Flex Weather Protection Roof LGS
Faster protection
A weather protection roof makes the jobsite more independent of weather and precipitation but it is not always easy to use and also very often subjected to high operational demands.
PERI has been working on the solution – with a motor and heating. The PERI Weather Protection Roof LGS on the basis of the LGS Lattice Girder System has long since found its place in many construction projects as a lightweight construction with large spans and safe operability. The advantage of having a large-sized cover, however, makes planning difficult and unwanted loads such as snow and ice to a potential problem. For winding and unwinding the sheeting, PERI now offers with a solution complete with an electric motor which significantly simplifies the operation. A concept for heating the keder sheeting will also be presented: integrated heating wires ensure that snow accumulation is avoided during the colder season.
Maximum flexibility for scaffolding construction
PERI UP Scaffolding Systems for industrial usage
For use in industry, a scaffolding system must be extremely adaptable and quick to mount. At the same time, all working areas must fulfil the very high requirements for occupational safety. The fact that the flexible PERI UP Flex Modular Scaffolding System optimally meets all prerequisites has been proven in countless projects.
Currently, large amounts of materials are being used in the Northwest Redwater Project in Canada – the world's most advanced oil sands refinery. Here, in addition to important safety issues, the focus is on time and cost reductions during the scaffold erection work. PERI has been supporting the internationally active EPC company with 3D planning services as well as with a control software for ensuring an optimized combination of scaffold planning and scaffold execution.
The versatile range of additional system components for specialized applications, such as suspended scaffolds, are continuously adapted to match the corresponding needs of the users. The high material utilization of standard components with a high level of execution efficiency can be seen as a great success in this respect. Also finding increasing use is the combination of PERI UP with the VARIOKIT Engineering Construction Kit. The uniform system grid arrangement, standardized connecting means and the option of renting of all system components make project-specific planning extremely cost-effective. At bauma 2016 in Munich, the advantages and possibilities will be explained and highlighted through a special exhibit.
PERI expands its production capacities for scaffolding systems
Purchase of Silvergreen facility in Günzburg, Germany
The Weissenhorn-based company PERI has announced the purchase of the Silvergreen site in Günzburg. The new location will complement the main plant in Weissenhorn as the expansion possibilities there are very limited.
As part of the company´s successful strategy in the scaffolding sector and the resulting increase in sales volumes, PERI urgently requires additional production capacity. However, at the headquarters in Weissenhorn, the currently available areas earmarked for expansion have been reserved for the expected future growth of the central administration as well as the German PERI subsidiary. Also for the core activity of formwork production in Weissenhorn, all reserve areas must be kept for future growth. As the family business knows and appreciates the advantages provided in the region, in particular the supply of highly skilled qualified workers as well as reliable suppliers, the site acquired in Günzburg, approx. 25 km away from Weissenhorn, presents an ideal complement. In the future, the PERI Group´s main scaffolding manufacturing facility will be based at this 135,000 m² area. The manufactured scaffolding systems are highly appreciated worldwide by customers from the industry and the construction sector due to the simple handling and high safety standards.
Leonhard Braig, Managing Director for Products and Technology at PERI stressed that the existing production in Weissenhorn will continue as before. "The purchase of the Silvergreen site marks for us a further important step as part of our growth strategy in the scaffolding market. We take a long-term approach, and the location based in Günzburg creates the framework conditions required for future corporate growth."
PERI considers the location of the plant as a particular advantage. On the one hand, it is a short distance from the headquarters in Weissenhorn and, on the other, it has optimal accessibility from a logistics perspective though the direct connection to the A8 motorway. During the course of this year, it is planned to commence production of scaffolding components; the new facility will create new jobs for around 90 skilled personnel.
The successful growth strategy adopted by PERI is also reflected in the figures. In 2015, PERI was able to increase turnover by 13 % thus surpassing its own sales record established in 2008. For Dr. Fabian Kracht, Managing Director for Finance and Organization, it is no coincidence. "Through the early and consistent internationalization strategy that was implemented, PERI could participate in and benefit from the growth markets in Asia, America and the Middle East. In the meantime, PERI realizes nearly 90 % of its turnover abroad. As a result of this international positioning, the company is also able to better compensate if faced with national economic crises as experienced in 2015, for example, in Brazil or Ukraine."