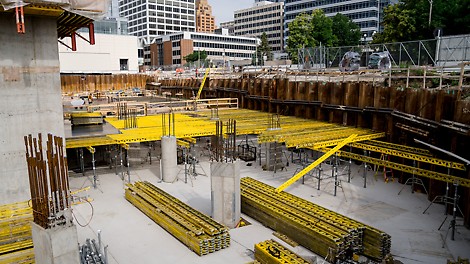
The Couture Milwaukee
Milwaukee, WI, United States
Lakefront Destination
Touted as the state of Wisconsin’s largest residential building once it is completed, The Couture replaces an underused transit center at Milwaukee’s Lakefront Gateway Project with a multimodal transit hub and apartment complex. The 44-story skyscraper was designed as a key thoroughfare connecting the lakefront and cultural amenities within downtown Milwaukee.
The first three levels of the 782,000-square-foot tower include a mix of public services, including lobbies, retail, ground-level transit concourse, parking, and a rooftop park. The fourth floor is home to private amenities for residents, including a pool and a hot tub. The tower’s 318 apartment units are in the remaining upper levels.
The Couture will help generate income through tax revenue and thousands of jobs for the city, helping Milwaukee continue to thrive. The tower will also be home for new downtown residents and deliver 50,000 square feet of high-end retail and restaurants to the neighborhood.
As the project team designed the tower and engineered systems to bring it to life, Findorff turned to the expertise of PERI USA for formwork, climbing systems, and shoring for safe and efficient construction.
Connecting with PERI Expertise
A customer of PERI since 1998, Findorff trusted the engineering support and product safety PERI delivered to the jobsite to realize this new development. In collaboration with the project team, PERI engineered a full package for formwork and scaffolding that allowed Findorff to rent any components they did not own. The first step was a trip to Chicago to a PERI jobsite to see the systems needed for the project in use and meet with that project team to hear about their experience.
The tight inner core presented potential for challenges in forming the tower. The PERI ACS Core 400 self-climbing system solved those challenges and enabled the crew to utilize hydraulic stripping and relief of the forms to move formwork efficiently and safely. Used on the super structure of the high rise and the elevator core forms, the self-climbing system allowed the crew to form one floor every four days on floors five through 44.
The ACS Core 400 self-climbing formwork system was designed for the U.S. market with a high-capacity, single-stroke cylinder that climbs to the next level in only 20 minutes. The system features spacious roll-back areas for the formwork and large platforms to enhance safety in worker areas.
For the core of the building, the project team specified 6,300 square feet of VARIO Wall Formwork. The girder wall formwork components can be freely selected, enabling the crew to adapt to the specific requirements of the building.
Findorff selected 8,000 square feet of MAXIMO and 5,000 square feet of TRIO formwork system to complete the shear walls with maximum productivity. Since Findorff owns both systems, crews came to the project with a familiarity of the user-friendly systems, and use of the systems offered cost savings on additional component rentals and time savings on learning new systems.
MAXIMO accelerates formwork operations with one-sided tie installation and optimized tie points to reduce working time by 50 percent. The centrally arranged tie points result in a regular joint and tie pattern both horizontally and vertically and provide an improved concrete finish.
TRIO ensures simple shuttering procedures and reduced shuttering times. With six different widths of standard panels, TRIO provides easy handling and efficient logistics for versatile and productive forming.
For the tower slab shoring, the project team used 15,000 square feet of SKYTABLE to quickly form the cast-in-place floors of the tower. SKYTABLE offers the ideal solution for large slab areas on buildings with open facades and is always engineered to be project specific. With a remote-controlled lifting mechanism, SKYTABLE can be quickly and safely moved to other stories.
Crews used 33,000 square feet of GARAGEDECK to form the beam and slab post-tensioned garage and complete the parking levels. GARAGEDECK is engineered for the United States market and delivers a cost-effective structure with no design limitations in superior quality.
For shoring requirements across the project, the team used a combination of 2,000 MULTIPROP aluminum slab props, 1,300 PEP Alpha Post Shores, 120 vertical feet of PERI UP for stair tower application, and 60,000 square feet of M-Flex.
MUTLIPROP post shores can be used as individual props or in combination with MULTIPROP frames to create shoring towers under tables. The aluminum props weigh less than steel and feature a significantly higher load-bearing capacity.
PEP Alpha Post Shores are optimized to provide a strong, versatile prop to satisfy 80 percent of typical usage applications on everyday job sites. The Alpha props are equipped with the G-hook pinning connection at the inner tube for quick height adjustment.
PERI UP is flexible, safe, and offers fast shoring towers for complex load-bearing birdcage structures that are adaptable to suit almost all geometries. The towers are dimensionally stable and can be moved in large units by crane due to the high rigidity of the ledger connections.
Moving In
PERI USA began delivering product to the jobsite in the fall of 2021 and is expected to complete concrete construction on the tower in February 2023. The Couture is anticipated to open in the summer of 2024.
Architect: RINKA
Engineer: Thornton Tomasetti
Civil Engineer: GRAEF
Contractor: Findorff
The Project
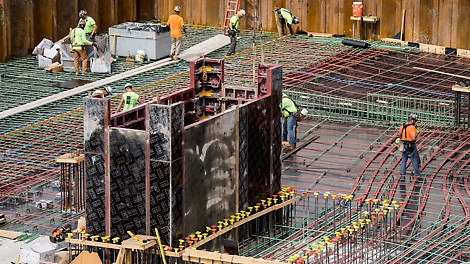
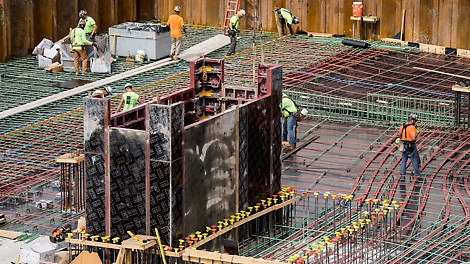
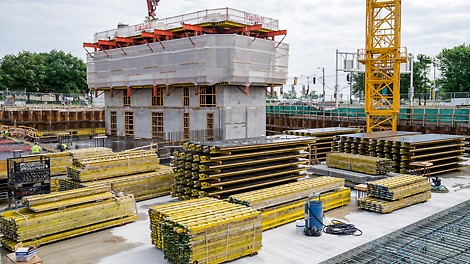
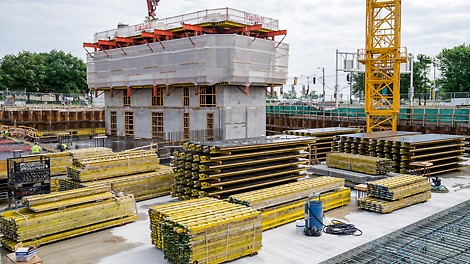
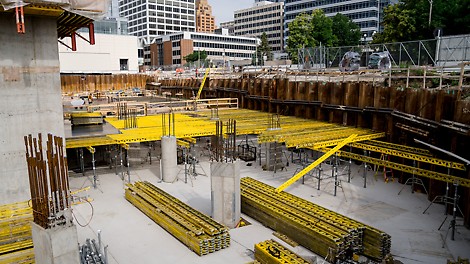
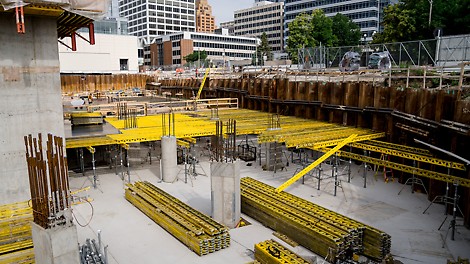


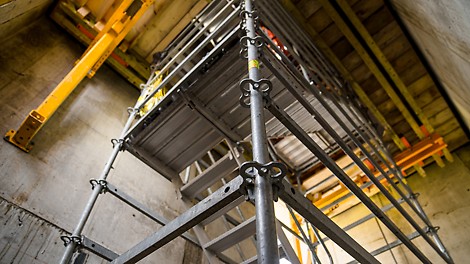
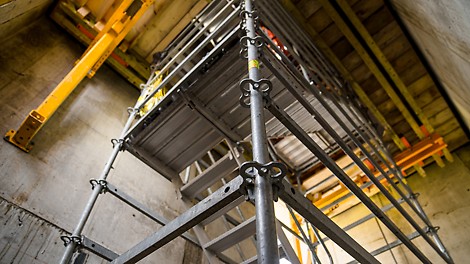
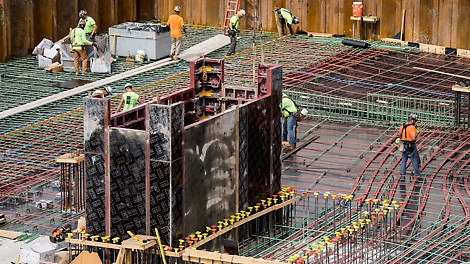
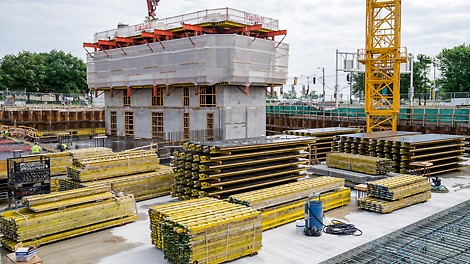
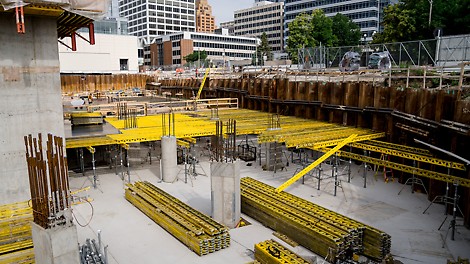

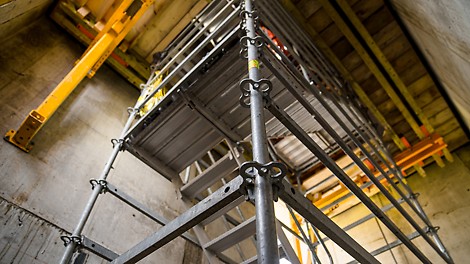
Project Information
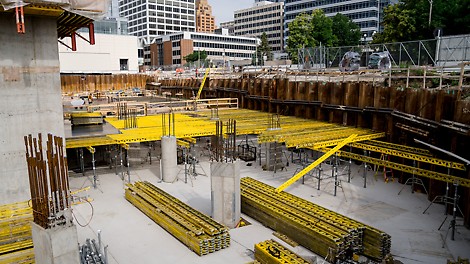
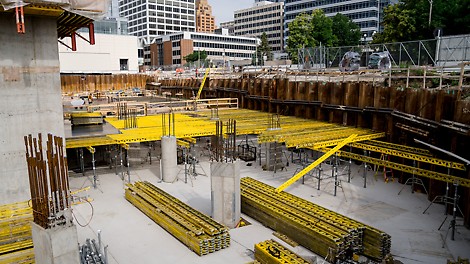